Our take on the Connected Kitchen.
A kitchen where every machine talks to you and tells you how it’s doing. Equipment that is remotely controlled and monitored, with data used to optimise product quality, maintenance visits, equipment uptime, or utility usage levels to maximise efficiency.
The Internet of Things. An expensive pipedream? That depends on who you ask. All the big equipment manufacturers are bringing out ‘smart’ kit – but there’s probably nothing wrong with the equipment you already have.
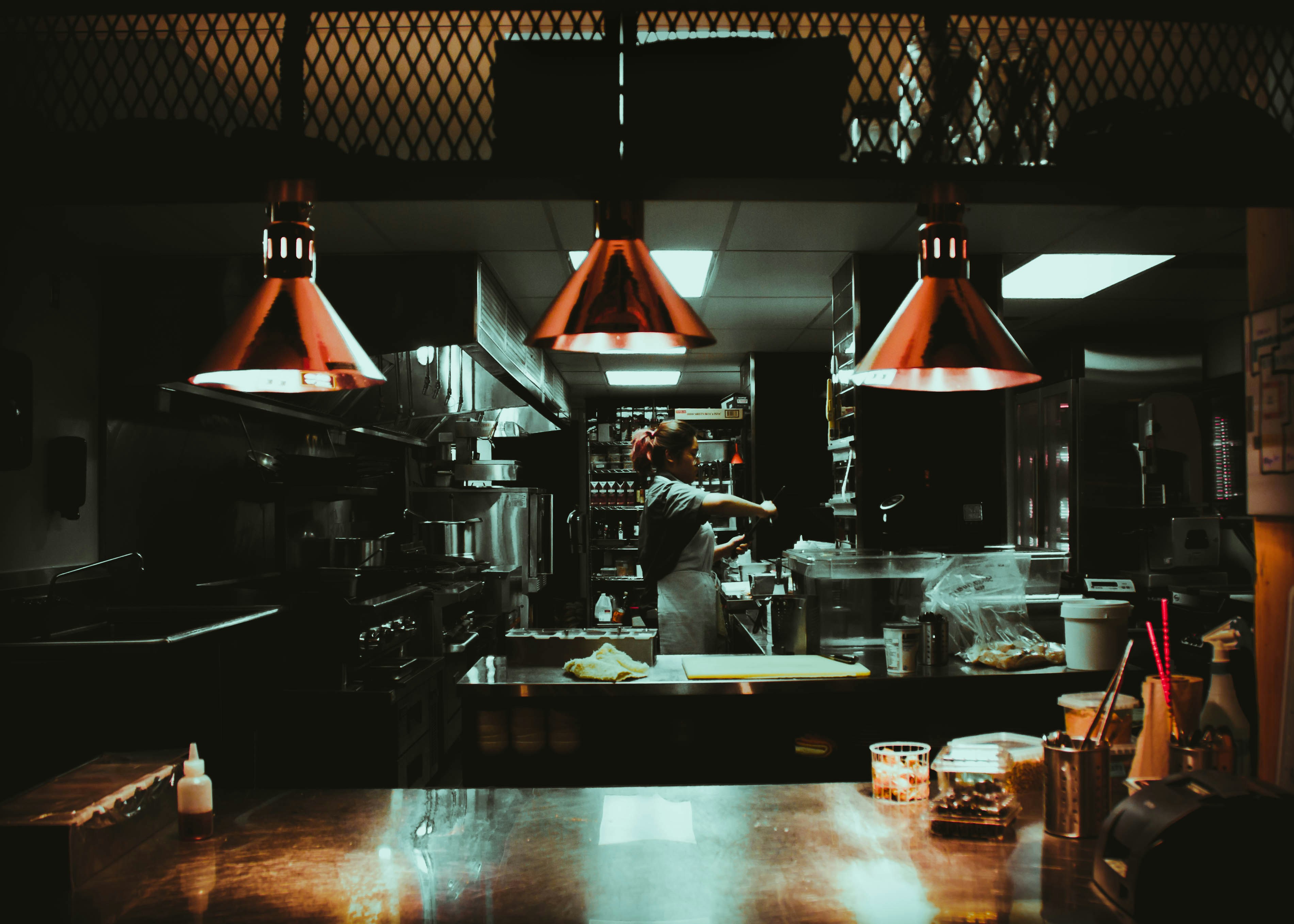
And while all that data sounds amazing, who’s going to interpret it and do something useful with it?
In truth, the Connected Kitchen is already here, but you’re probably not ready for it yet and the current economic outlook isn’t exactly conducive to spending a fortune on converting everything anyway.
So why not start small? Our sensors are agnostic – they’ll work on virtually everything you already have, making legacy equipment automatically ‘smart’. And all the data goes to the same place, so you can read it on a single portal. You choose what you want monitored and we’ll manage the data for you.
Just remember: If you don’t own your own data, eventually someone else will.
How It Works.
Discover the seamless process behind our technology. From start to finish, we ensure efficiency, reliability, and ease of use.
01
Installation
You decide what equipment you want monitored and we’ll install our real-time sensors on it.
Our installation team are endorsed and trusted by both Coca-Cola & McDonald’s who set a high bar when it comes to standards.
02
Live Data
The sensors report every 60secs, 24hours a day, 7 days a week via a Wifi or 4G gateway.
The data is sent securely to our Amazon Web Services (AWS) cloud platform where the key metrics (temperature, power etc) are displayed on our portal.
03
Alerts & Trouble Shooting
If an issue is detected, the system automatically sends an alert to any key people you’ve nominated or direct to your Service Company.
Our emails not only identify the problem but can provide troubleshooting tips to help solve the problem faster or preventing the problem getting worse.
04
Reporting & Analysis
Over time, the data builds up a picture of your equipment’s trend performance. We use this to provide benchmarks against which the performance can be judged – spotting issues before they become problems.
What we can monitor.
Built on our expertise in soft drinks, our technology has evolved to meet the needs of our customers. Our smart sensors can now monitor a wide range of metrics including:
Power consumption (Single phase & 3-phase)
Potable water volumes
Filter usage
Water pressures
Water temperatures/Boiler temperature output (Legionella record keeping)
Fridge/Freezer temperatures (HACCP)
Room temperatures & Air Quality
Soft drink quality
(to Coca-Cola Global standards)
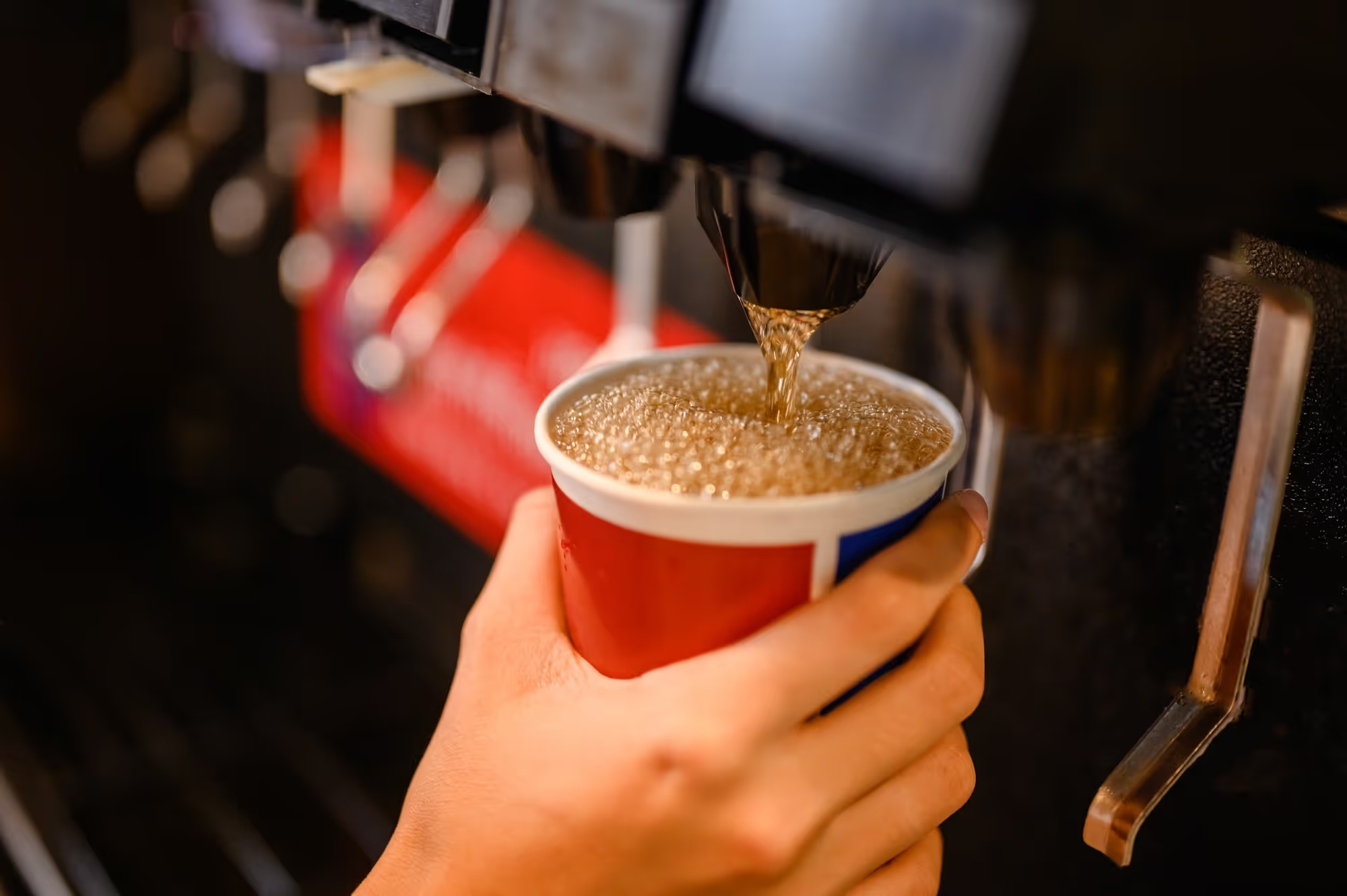
Why prevention matters.
We don’t just monitor your equipment—we prevent problems before they happen. We catch small issues early, saving you from costly repairs, downtime, and frustrated teams.
One investment you can’t afford not to make.
FAQs
Answers to some of the most frequently asked questions about Telemetry
Yes. Not only do we have an FSA Feasibility Study to prove it, but Food Safety Officers are usually very impressed by a business that can provide in-depth, independent, and tamper-proof HACCP data. The time savings alone can often justify the cost.
Yes. By optimising equipment performance, we can help reduce energy waste, water consumption, and unnecessary servicing — helping businesses operate more sustainably while lowering utility costs.
Tricky to answer this one because if it works well, the system will prevent expensive problems (or at least prevent problems becoming really expensive) so it’s hard to present a cast-iron ROI.
Only you know how often you have an expensive problem that could have been avoided, so the real question is whether you can afford NOT to have an early-warning system on your key equipment. In the long run, we’re confident that the savings from improved efficiency, fewer repairs, and reduced downtime make Telemetry an affordable and valuable investment for your business.
Yes. We’ve successfully worked with businesses in Europe & the USA. Our system is standardised ensuring that we can support companies in any European market. Working in the USA requires sensors that work on a different wavelength.
No, but any cost you think you can’t justify might be considered expensive. You pay for the number of sensors you need and then a low monthly subscription — usually less than the cost of a cup of coffee a day depending on how many sensors you have. We supply the gateway for free (but it remains our property because that way we’re responsible for it working).
We meet the strictest Global security standards as set by The Coca-Cola Company with encrypted transmissions and secure cloud storage.
We started doing just temperatures, but customers soon asked for more so we’ve expanded into lots of other areas. The short version is that if it produces data, we can normally extract it. Just ask.